Title: Why Aesthetic Design Fails Without Manufacturing Expertise (And How to Fix It)
Aesthetic design often fails without manufacturing expertise, leading to costly mistakes. Aesthetic design captivates consumers, drives brand loyalty, and differentiates products in crowded markets. However, focusing solely on visual appeal often leads to costly failures—products that look stunning in CAD software but crumble under real-world manufacturing constraints. For inventors, designers, and businesses launching new products, bridging the gap between aesthetic design and design for manufacture (DFM) is non-negotiable. Below, we explore why aesthetics fail without manufacturing expertise and how to fix these pitfalls to achieve cost reduction, manufacturing efficiency, and market success.
The High Cost of Ignoring Manufacturing Realities

Key Issues in Aesthetic-Only Design:
- Material Missteps: Visually appealing materials (e.g., transparent plastics) may lack durability or be incompatible with high-volume processes.
- Complex Geometries: Overly intricate shapes often require expensive tooling or manual assembly.
- Over-Engineering: Unnecessary features inflate production costs without adding value.
To avoid these pitfalls, manufacturing engineers must collaborate with designers from day one.
Rule 1: Why Aesthetic Design Fails Without Manufacturing Expertise & How DFM Solves It
Design for manufacture (DFM) ensures products are both beautiful and manufacturable. Start by:
- Simplifying geometries: Replace sharp angles with radii to ease molding.
- Standardizing components: Use common materials like ABS or polypropylene to cut costs.
- Simulating early: Run mold flow analyses during prototyping to catch flaws.
Example: A furniture company redesigned a chair leg with uniform wall thickness, reducing injection molding cycle times by 20%.
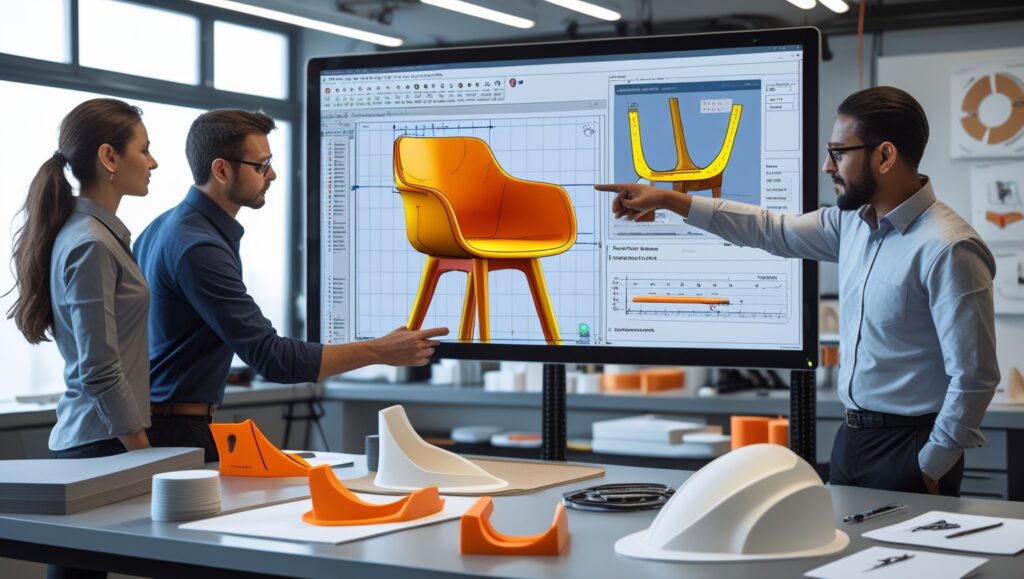
Rule 2: Partner with Manufacturing Engineers
Manufacturing engineers translate creative visions into producible designs. Their input helps:
- Optimize tolerances: Tight tolerances look precise but increase machining costs.
- Select processes: For instance, vacuum forming may suit large panels better than injection molding.
- Balance aesthetics and function: A textured grip on a tool can enhance usability without complicating molds.
Case Study: A medical device firm reduced tooling costs by 45% after engineers suggested consolidating four parts into two using snap-fits.
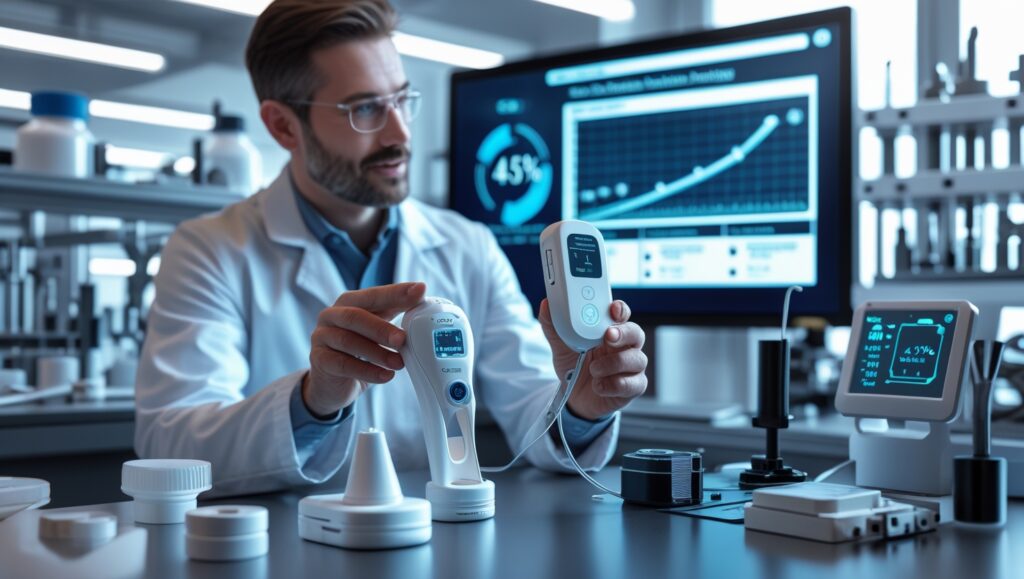
Rule 3: Prioritize Modular Design for Upgrades
Businesses updating product lines benefit from modularity. Design components that can be easily swapped or upgraded without overhauling entire systems.
Example: A consumer electronics brand uses standardized ports across devices, allowing seamless upgrades while maintaining a sleek aesthetic.
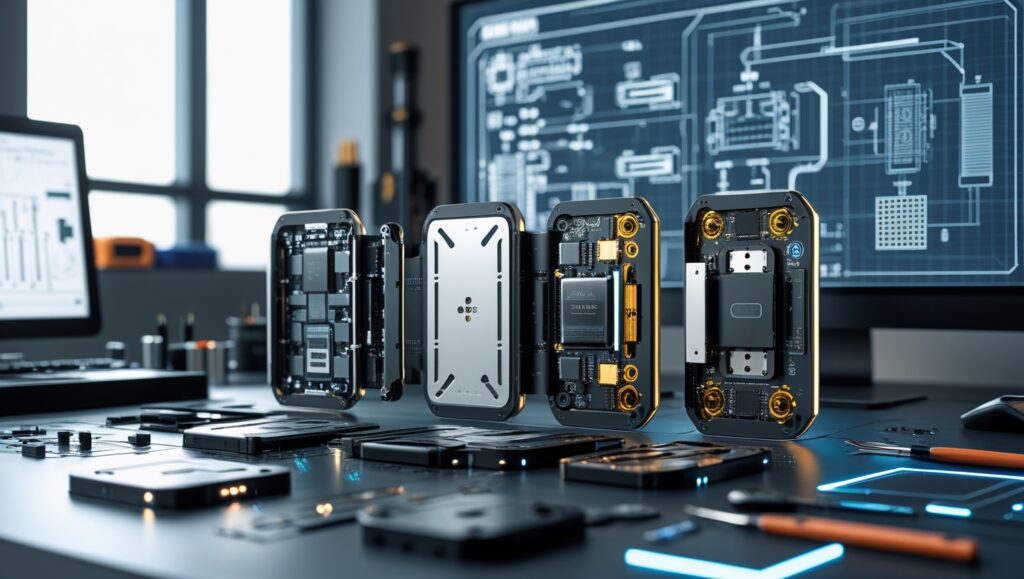
Rule 4: Leverage Advanced Tools
Software like CAD-integrated DFM checkers and AI-driven simulations identify manufacturability issues early. Tools to adopt:
- Generative design software: Balances aesthetics with structural efficiency.
- 3D printing: Prototype complex designs cost-effectively before committing to tooling.
Pro Tip: Use topology optimization to remove excess material while preserving visual appeal.
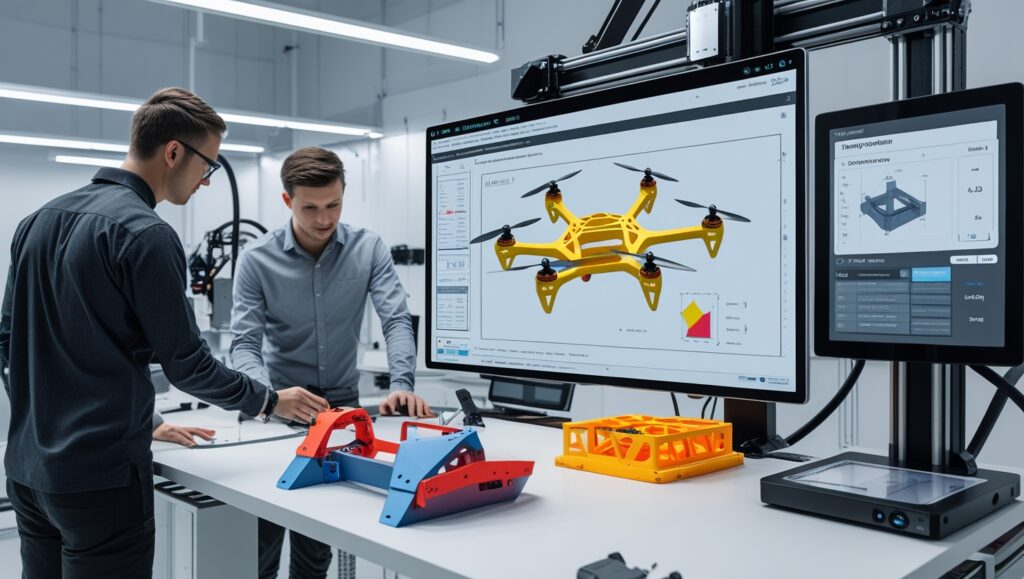
Rule 5: Educate Your Team
Aesthetic designers often lack manufacturing literacy. Invest in training, such as BP Nel Consulting’s DFM courses, which cover:
- Material selection for mass production.
- Cost-effective design tweaks.
- Collaboration strategies for cross-functional teams.
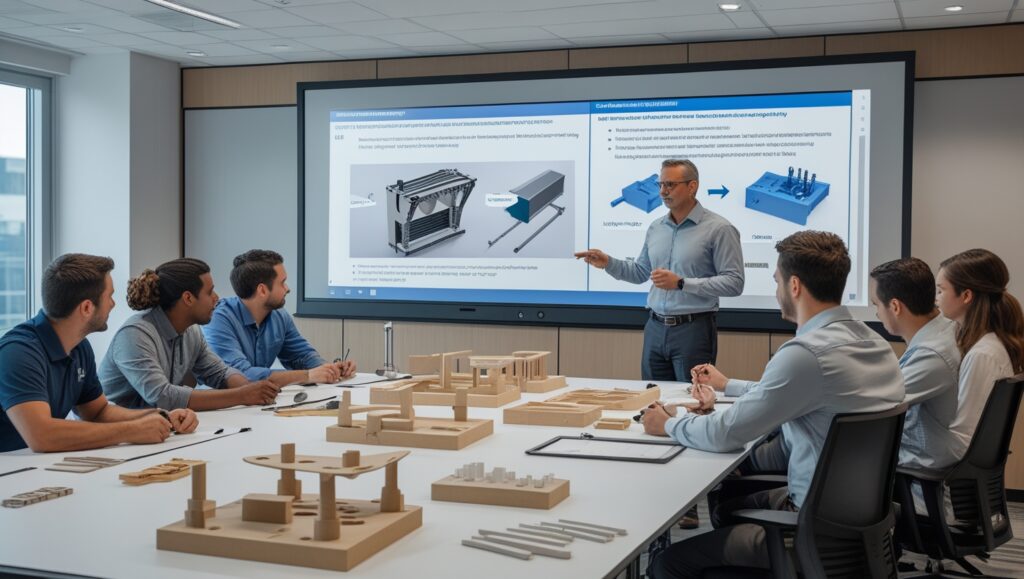
How to Fix Aesthetic Design Failures: A Step-by-Step Guide
- Audit Existing Designs: Identify features causing delays or defects.
- Prototype Rigorously: Test aesthetics against manufacturing limits.
- Iterate with Feedback: Involve engineers in every design sprint.
- Monitor Metrics: Track scrap rates, cycle times, and ROI per design change.
Conclusion: Marry Beauty with Practicality
Aesthetic design wins attention, but manufacturing expertise ensures products survive the real world. By embedding DFM principles early, collaborating across teams, and leveraging modern tools, businesses can achieve cost reduction, boost manufacturing efficiency, and launch products that are both stunning and sustainable.
At BP Nel Consulting, we specialize in turning visionary designs into manufacturable realities. Contact us for a free design audit or explore our online DFM courses to equip your team with critical skills.