From CAD to Factory Floor: How DFM Saves Time and Money in Product Design
In today’s competitive market, the journey from a product’s conceptualization to its mass production is fraught with challenges. One critical methodology that bridges the gap between design and manufacturing is Design for Manufacturing (DFM) in product design. By integrating DFM principles early in the design process, companies can significantly reduce costs, accelerate time-to-market, and enhance product quality. This article delves into how DFM saves time and money in product design, guiding you from the initial CAD models to the factory floor.
Understanding DFM: A Brief Overview
Design for Manufacturing (DFM) is a systematic approach that emphasizes designing products to simplify manufacturing processes, thereby reducing production costs and complexities. By considering manufacturing constraints during the design phase, potential issues can be identified and addressed before they escalate into costly problems during production. Check online DFM Courses
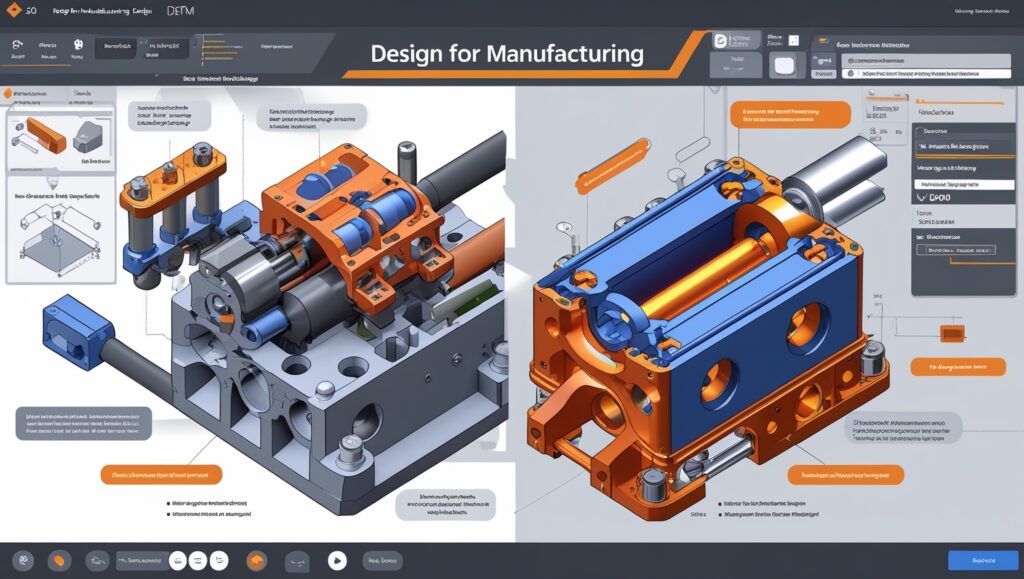
The Financial Implications of Neglecting DFM
Overlooking DFM principles can lead to significant financial repercussions:
Increased Production Costs: Complex designs may require specialized tooling or intricate assembly processes, inflating manufacturing expenses.
Extended Time-to-Market: Unforeseen manufacturing challenges can cause delays, allowing competitors to capture market share.
Elevated Scrap Rates: Designs that are difficult to manufacture often result in higher defect rates, leading to material wastage and additional costs.
For instance, a manufacturer who resisted applying DFM principles faced prolonged production times and costly delays, ultimately leading to a decline in sales and profitability.
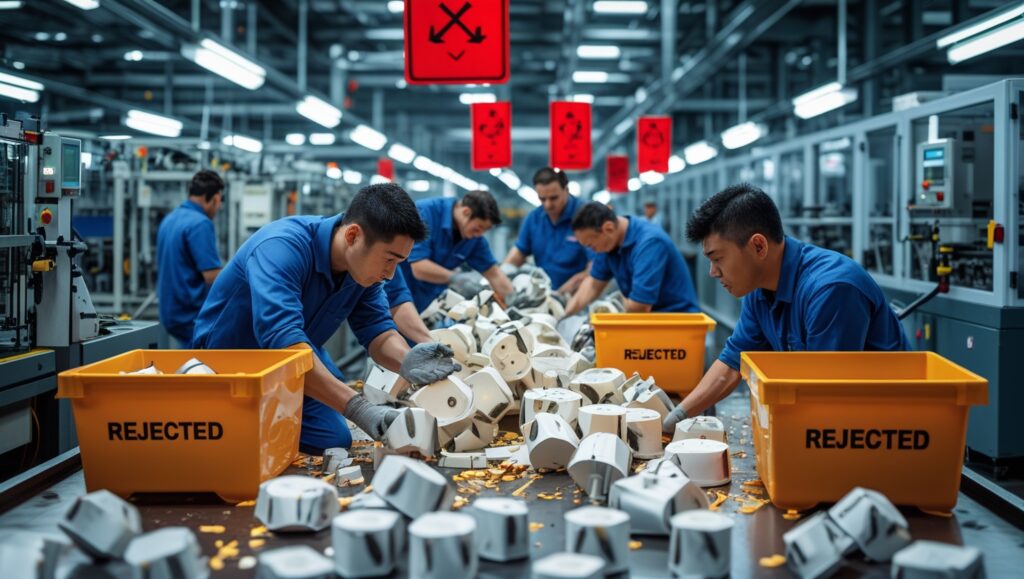
How DFM Saves Time and Money
Implementing DFM principles offers several tangible benefits:
1. Simplified Designs
By simplifying product designs, manufacturers can reduce the number of components, minimize assembly steps, and decrease the likelihood of errors. This streamlining leads to faster production cycles and reduced labor costs.
2. Standardized Components
Utilizing standard components wherever possible reduces the need for custom parts, lowering procurement costs and simplifying inventory management.
3. Early Detection of Manufacturing Issues
Incorporating DFM early in the design phase allows for the identification and resolution of potential manufacturing challenges, preventing costly redesigns and production halts.
4. Enhanced Collaboration
DFM fosters collaboration between design and manufacturing teams, ensuring that both perspectives are considered, leading to more feasible and cost-effective product solutions.
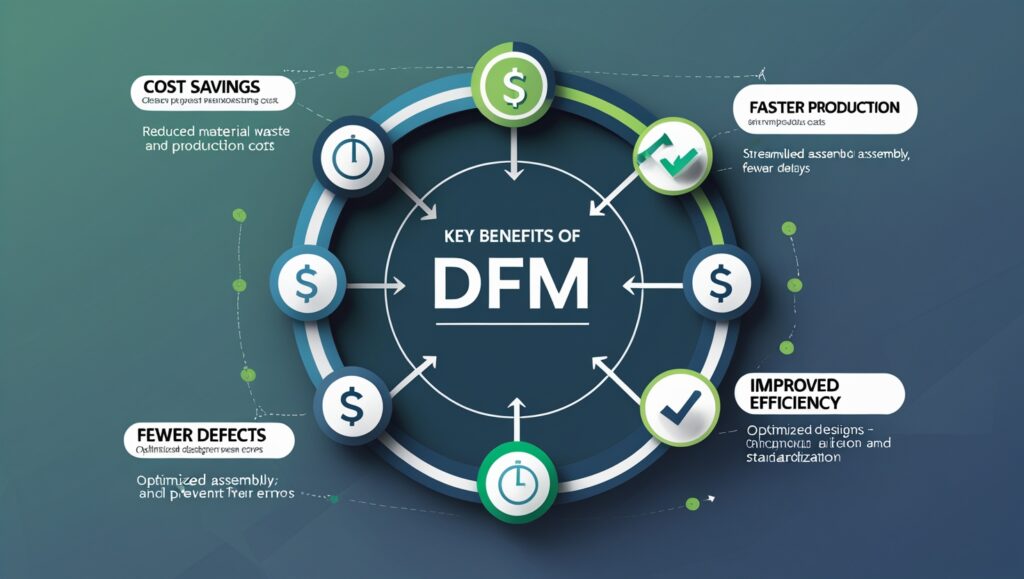
Case Study: The Impact of DFM on Product Success
A smartphone manufacturer integrated DFM principles from the initial design phase, resulting in a 30% reduction in assembly time for their latest model. This efficiency not only reduced labor costs but also accelerated the product’s time-to-market, providing a competitive advantage.
Implementing DFM: A Step-by-Step Guide
To effectively incorporate DFM into your product design process, consider the following steps:
1. Cross-Functional Team Formation
Assemble a team comprising designers, engineers, and manufacturing specialists to ensure diverse perspectives are integrated from the outset.
2. Define Manufacturing Constraints
Clearly outline the limitations and capabilities of your manufacturing processes to guide design decisions.
3. Design Evaluation
Regularly assess designs against manufacturing constraints, making necessary adjustments to enhance manufacturability.
4. Prototype Testing
Develop prototypes to validate design choices and identify potential manufacturing issues before full-scale production.
5. Continuous Improvement
Establish a feedback loop between the design and manufacturing teams to continually refine processes and designs for optimal efficiency.
The Role of Technology in DFM
Advancements in technology have significantly bolstered DFM practices:
1. CAD Software
Modern Computer-Aided Design (CAD) tools enable designers to create detailed models that consider manufacturing constraints, facilitating smoother transitions from design to production.
2. Simulation Tools
Simulation software allows for virtual testing of designs under various manufacturing scenarios, identifying potential issues without the need for physical prototypes.
3. Additive Manufacturing
3D printing enables rapid prototyping, allowing for quick iterations and validations of design concepts, reducing development time and costs.
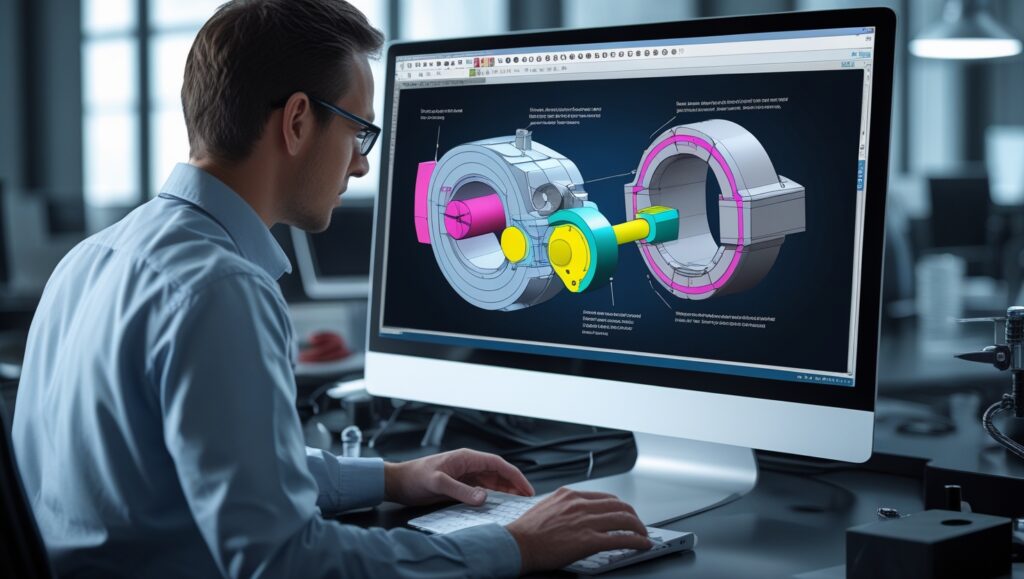
Challenges in Implementing DFM
While the benefits of DFM are substantial, several challenges may arise:
1. Resistance to Change
Teams accustomed to traditional design processes may hesitate to adopt DFM principles, necessitating cultural shifts and training.
2. Initial Investment
Implementing DFM may require upfront investments in training and technology, which can be a barrier for some organizations.
3. Balancing Aesthetics and Manufacturability
Ensuring that products are both visually appealing and manufacturable can be challenging, requiring close collaboration between design and manufacturing teams.
Overcoming DFM Implementation Challenges
To address these challenges:
Provide Training: Educate teams on the benefits and methodologies of DFM to foster acceptance and proficiency.
Demonstrate ROI: Highlight successful case studies and potential cost savings to justify initial investments.
Foster Collaboration: Encourage regular communication between design and manufacturing teams to balance aesthetic desires with manufacturing realities.
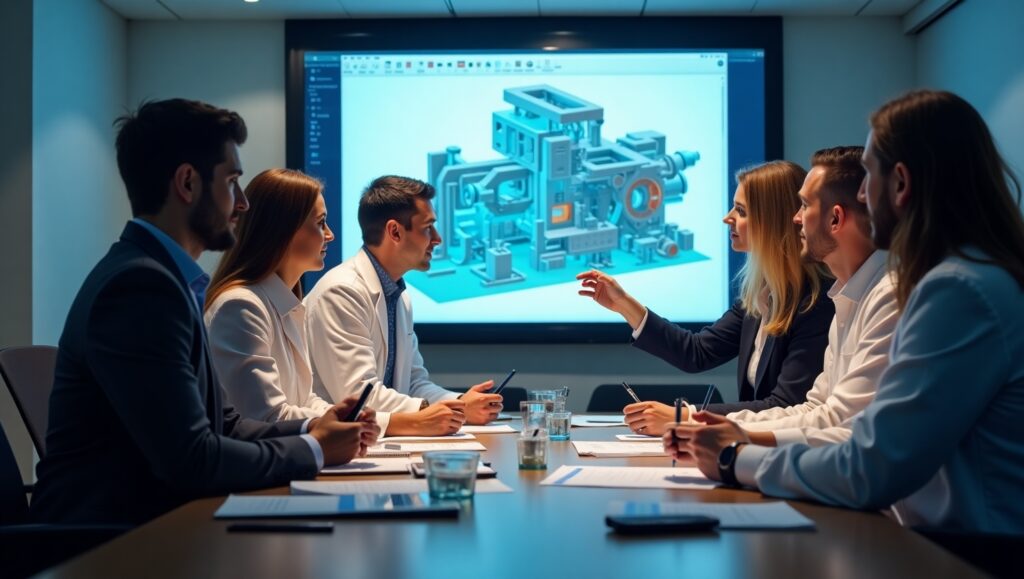
Conclusion: Embracing DFM for Competitive Advantage
Integrating Design for Manufacturing (DFM) in product design from the earliest stages of product development is crucial for reducing costs, accelerating production timelines, and ensuring product quality. By fostering collaboration, leveraging advanced technologies, and committing to continuous improvement, organizations can navigate the complexities of modern manufacturing and achieve sustained success.
At BP Nel Consulting, we specialize in transforming innovative ideas into manufacturable products. With over 29 years of experience, we assist clients in reducing production costs, enhancing product quality, and accelerating time-to-market. Our expertise spans various industries, including consumer products, medical devices, sports equipment, and more. By partnering with us, you can ensure that your designs are not only innovative but also optimized for efficient manufacturing.