Title: How to Design for Injection Molding: 7 Rules to Slash Production Costs
Injection molding stands as one of the most efficient methods for mass-producing plastic components, but its success hinges on how well a product aligns with design for manufacturability (DFM) principles. Poor design choices often lead to extended cycle times, material waste, and costly tooling adjustments. For inventors, engineers, and businesses aiming to optimize manufacturing efficiency and achieve cost reduction, mastering design for injection molding is essential. Below, we break down seven actionable rules to refine your approach to part geometry optimization and streamline production.
1. Prioritize Uniform Wall Thickness
Consistent wall thickness is foundational to product design for injection molding. Variations in thickness disrupt cooling rates, leading to defects like warping, sink marks, or internal stresses. For example, thick sections cool slower than thin ones, creating uneven shrinkage that compromises part quality.
Most thermoplastics perform best with wall thicknesses between 1.5 mm and 3 mm. If thicker sections are unavoidable, use gradual transitions (e.g., tapered ribs) to minimize abrupt changes. This approach reduces cycle times, optimizes material usage, and enhances manufacturing efficiency.
Pro Tip: Use simulation software to analyze wall thickness distribution before finalizing your design.
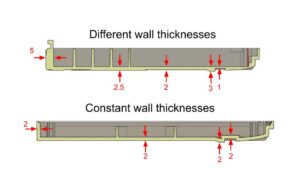
2. Incorporate Draft Angles for Easy Ejection
Draft angles—slight tapers on vertical walls—are non-negotiable for smooth part ejection. Without them, friction between the part and mold can damage surfaces or force operators to manually pry out components, slowing production.
Aim for 0.5–2 degrees of draft on most features. Textured surfaces may require up to 5 degrees due to increased friction. Apply draft to both internal and external walls to extend mold life and reduce long-term costs.
Real-World Example: A client reduced ejection failures by 70% after adding 1.5-degree drafts to their medical device housing.
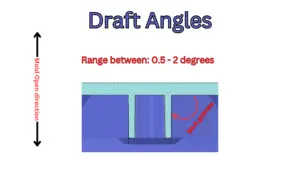
3. Optimize Ribs and Gussets for Strength
Ribs and gussets add rigidity without increasing wall thickness, but improper design causes sink marks or air traps. Follow these guidelines:
- Keep rib thickness below 60% of the adjacent wall.
- Maintain a height-to-thickness ratio of 3:1.
- Align ribs with material flow direction to minimize resistance.
For instance, a consumer electronics company eliminated sink marks in a laptop bezel by reducing rib thickness from 2.5 mm to 1.8 mm.
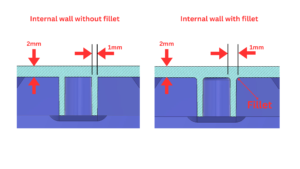
4. Replace Sharp Corners with Radii
Sharp corners create stress concentrations and impede material flow, increasing failure risks. Incorporate radii of at least 0.5x the wall thickness to:
- Improve material distribution.
- Reduce mold wear.
- Minimize turbulence during filling.
A 1 mm radius on a 2 mm wall, for example, ensures smoother flow and fewer rejects. This simple adjustment supports cost reduction by cutting scrap rates.
5. Strategize Gate Placement
Gate location determines how molten plastic fills the mold. Poor placement leads to weld lines, air traps, or uneven packing. To avoid defects:
- Position gates on non-visible surfaces.
- Use simulation tools to predict flow patterns.
In a recent project, relocating the gate from the center to the edge of a gear component eliminated weld lines and improved structural integrity.
6. Minimize Undercuts to Simplify Tooling
Undercuts—features that block part ejection—demand complex (and expensive) sliding molds or collapsible cores. Redesign them using DFM-friendly solutions like:
- Snap-fits for enclosures.
- Living hinges for folding parts.
For low-volume production, aluminum molds with interchangeable inserts offer a cost-effective workaround. However, always weigh this against long-term manufacturing efficiency goals.
7. Select Materials Wisely
Material choice impacts both part performance and production costs. For example:
- Polypropylene (PP): Excellent flow properties reduce injection pressure.
- ABS: Balances strength and aesthetics for consumer goods.
- PEEK: High-performance but requires costly high-temperature tooling.
Collaborate with material suppliers early to align resin properties with your product design and budget.
Boost Your Skills with BP Nel Consulting’s Injection Molding Course
Mastering design for injection molding requires deep technical knowledge—and BP Nel Consulting has crafted a solution. Our self-paced online course, Design for Injection Molding: From Concept to Production, equips beginners with practical skills through 18 in-depth lectures. Key modules include:
- Wall Thickness Optimization: Avoid warping and sink marks.
- Gate and Runner Design: Achieve flawless fills.
- Material Selection Strategies: Balance cost and performance.
- Moldability Analysis: Use simulation tools like a pro.
Whether you’re an inventor prototyping a new idea or an engineer refining production workflows, this course empowers you to design parts that are functional, cost-effective, and manufacturable. Order here
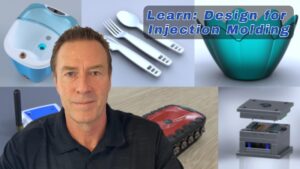
Conclusion: Design Smarter, Produce Faster
Injection molding doesn’t have to be a costly bottleneck. By integrating these seven rules into your design for manufacturability process, you can slash production expenses, accelerate time-to-market, and deliver higher-quality products.
At 3DDFM, we combine decades of mechanical engineering expertise with cutting-edge DFM strategies to transform your concepts into manufacturable designs. For hands-on learning, enroll in our online course or schedule a consultation to optimize your next project.