3D Printing vs Injection Molding: When to Choose Which (and Why)
In the world of manufacturing, two technologies often stand out: 3D printing and injection molding. Each has unique advantages and is best suited for different applications. Whether you are developing a prototype, launching a product, or scaling up production, choosing the right manufacturing method is critical. In this guide, we’ll explore the differences between 3D printing vs injection molding, when to use each, and why one may be better suited for your project than the other.
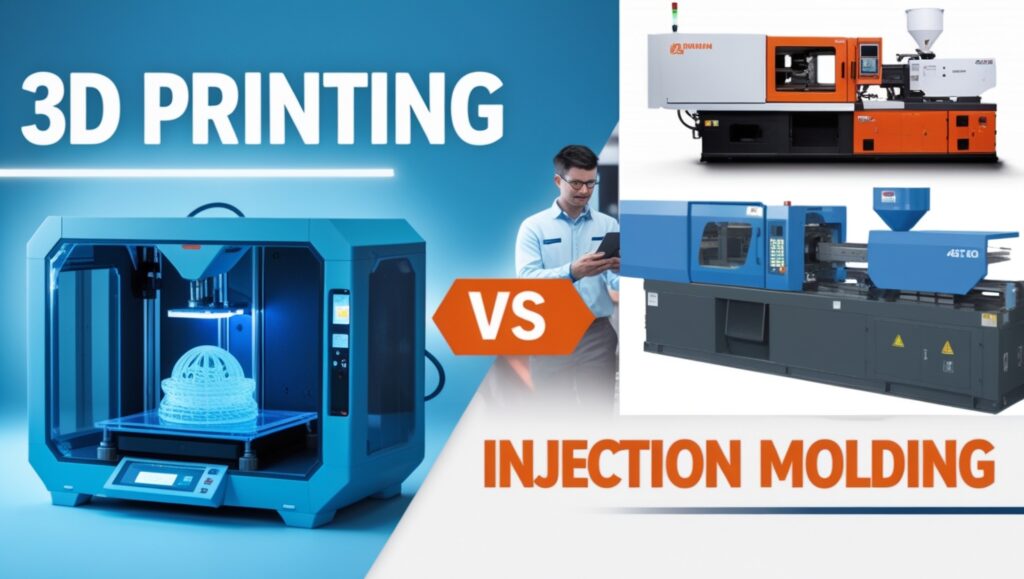
Understanding 3D Printing
3D printing, also known as additive manufacturing, is a process that builds objects layer by layer from a digital file. This technique allows for creating highly detailed and complex designs without the need for expensive molds or tooling. Unlike traditional manufacturing, which often involves cutting, molding, or shaping materials, 3D printing builds objects from the ground up, offering unparalleled design flexibility.
Advantages of 3D Printing
Rapid Prototyping – Since no molds are required, 3D printing allows for quick iterations and modifications, making it ideal for product development.
Low Setup Costs – Unlike injection molding, 3D printing does not require an expensive upfront investment in molds, which can be a game-changer for startups and innovators.
Complex Geometries – Designs that are difficult or impossible to produce with traditional manufacturing methods can be easily created with 3D printing.
Customization – Ideal for producing unique, personalized products without increasing costs, making it highly flexible for small production runs.
Reduced Waste – As an additive manufacturing process, 3D printing generates minimal material waste, making it a more sustainable option compared to subtractive manufacturing.
Variety of Materials – Modern 3D printers support a wide range of materials, including plastics, resins, metals, and even ceramics, making it a viable option for different industries.
Speed – In some cases, 3D printing can produce parts in a matter of hours, whereas traditional manufacturing might take weeks.
When to Choose 3D Printing
3D printing is the best option when you need:
✔ Prototypes for testing and validation before moving to mass production. ✔ Small-batch production of a few hundred units where mold costs would be too high. ✔ Highly complex or customized parts that are not feasible with traditional molding techniques. ✔ Lightweight structures that require intricate internal supports. ✔ Fast turnaround for new design iterations without costly retooling. ✔ Sustainability by reducing material waste and energy consumption.
However, 3D printing is not always the ideal choice for large-scale production due to its slower printing speeds and higher cost per unit compared to injection molding.
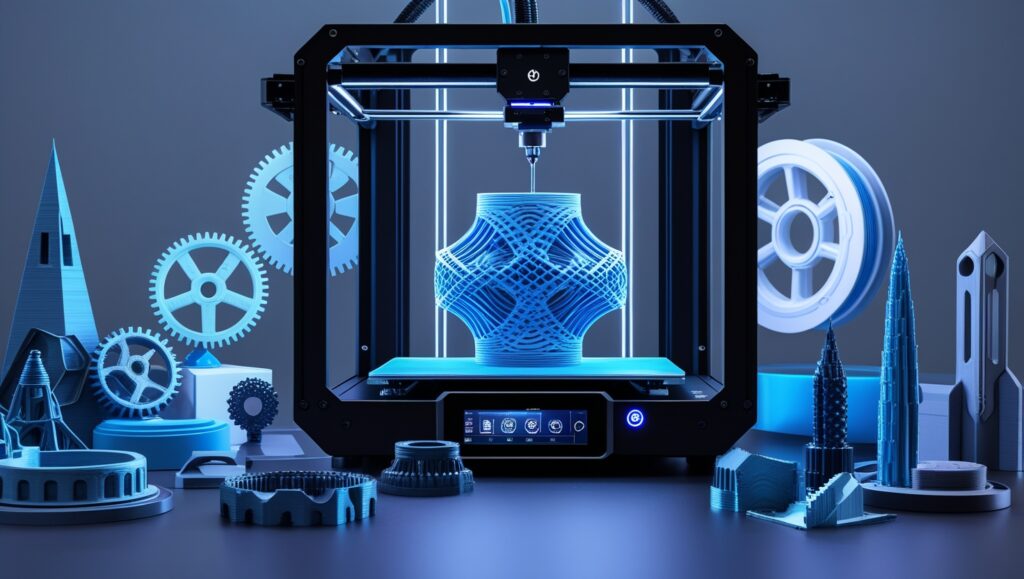
Understanding Injection Molding
Injection molding is a manufacturing process in which molten material, typically plastic, is injected into a mold cavity, cooled, and solidified into the final shape. This technique is widely used for high-volume production due to its efficiency and cost-effectiveness at scale.
Advantages of Injection Molding
High Production Efficiency – Once the mold is created, production is incredibly fast, allowing thousands of units to be manufactured per hour.
Consistent Quality – Injection molding ensures uniformity in mass production, reducing variations between units.
Lower Per-Unit Cost at Scale – While mold creation is expensive, the cost per unit decreases significantly with higher production volumes.
Wide Material Selection – A variety of plastics, composites, and other materials can be used, providing flexibility for different applications.
Durability and Strength – Injection molded parts often have better mechanical properties compared to 3D-printed parts.
Scalability – Injection molding is highly scalable, making it the preferred method for producing millions of identical parts.
Surface Finish & Aesthetics – The process delivers smooth surfaces and detailed features, often requiring little to no post-processing.
When to Choose Injection Molding
Injection molding is the best option when you need:
✔ Mass production of thousands or millions of identical parts. ✔ Durable and strong components that need to withstand stress and wear. ✔ Consistent and high-quality parts without variations between units. ✔ Lower cost per unit for large-scale manufacturing. ✔ High-speed production with minimal labor intervention. ✔ Smooth finishes without additional post-processing work.
However, injection molding requires expensive mold creation, making it less practical for small-scale or custom projects.
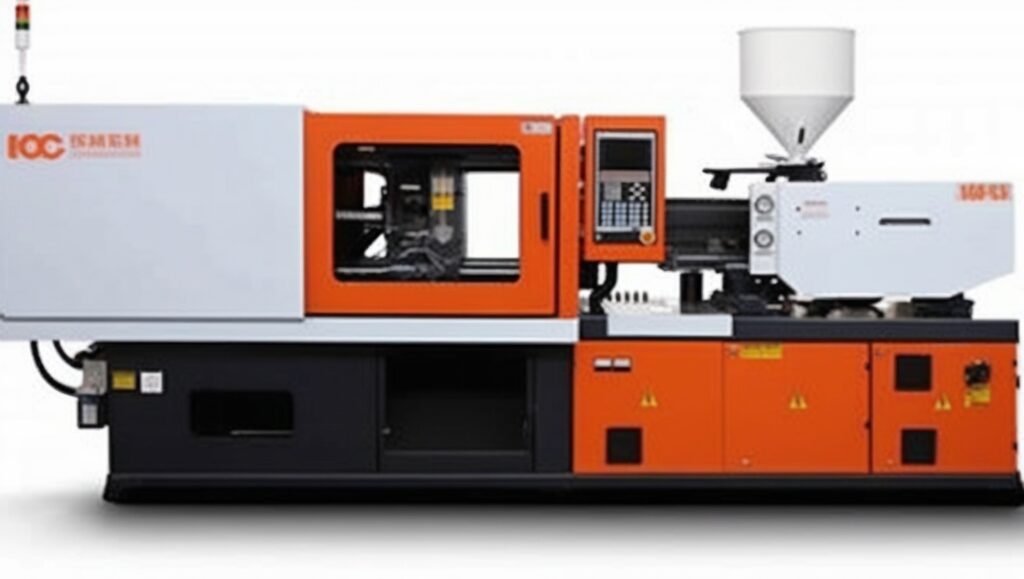
3D Printing vs Injection Molding: Which One Should You Choose?
The decision between 3D printing and injection molding depends on several key factors:
1. Production Volume
If you need low-volume production (less than 1,000 units), 3D printing is the better choice.
If you require high-volume production (10,000+ units), injection molding is more cost-effective.
2. Cost Considerations
3D printing has lower upfront costs but higher cost per unit as production scales.
Injection molding has high initial mold costs but lower per-unit cost for large-scale manufacturing.
3. Complexity of Design
3D printing excels at complex geometries and intricate details without additional tooling.
Injection molding is better for simpler, mass-produced parts with standard shapes.
4. Lead Time
3D printing offers faster turnaround times for prototypes and low-volume production.
Injection molding requires mold development, which can take weeks, but once molds are ready, production is rapid.
5. Material Requirements
3D printing is ideal for prototypes and lightweight structures, offering flexibility in material use.
Injection molding is preferred for strong, durable parts that require high-performance materials.
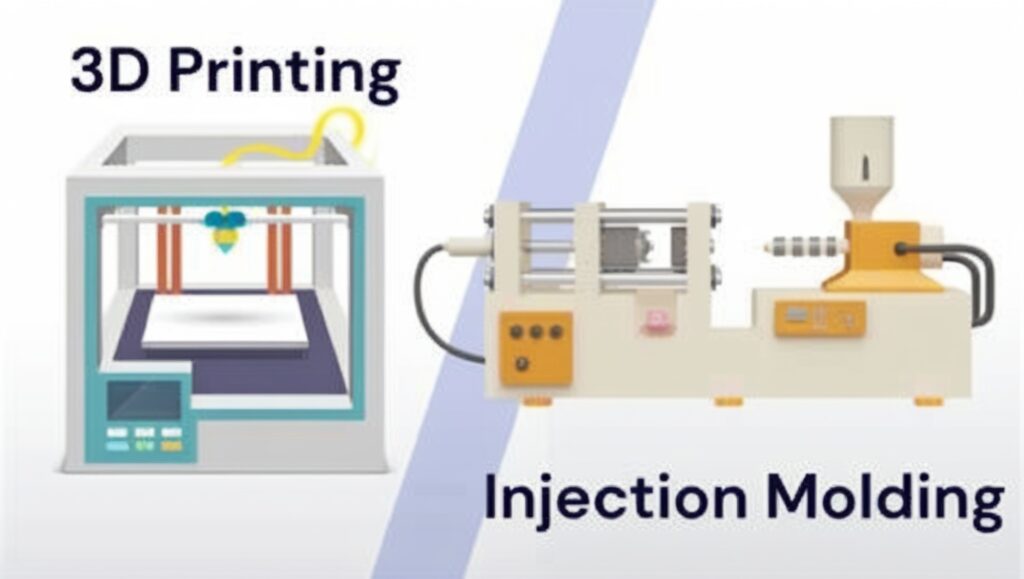
Real-World Applications
Aerospace & Automotive: 3D printing is used for lightweight, complex components while injection molding is used for mass production of durable parts.
Medical Industry: Custom prosthetics and dental implants benefit from 3D printing, while injection molding is used for mass-producing syringes and surgical instruments.
Consumer Goods: Toys, electronic casings, and packaging are ideal for injection molding, while 3D printing is used for niche, customized products.
Case Study: A Hybrid Approach
A startup developing a new wearable device used 3D printing for early prototypes, allowing them to iterate rapidly. Once they finalized the design, they switched to injection molding for mass production, lowering per-unit costs. This hybrid approach maximized both speed and cost efficiency.
Future Trends in 3D Printing & Injection Molding
AI-Driven Design Optimization: AI tools are making both technologies smarter, reducing material waste and improving efficiency.
New Materials: Advancements in bio-based plastics and carbon fiber-infused filaments are expanding the possibilities for both methods.
Automation & Robotics: Smart factories integrating robotics are making injection molding even faster, while AI-driven slicing software enhances 3D printing precision.
Conclusion: Making the Right Choice
Both 3D printing and injection molding have their advantages and disadvantages, and the right choice depends on your project’s needs. If you’re unsure, reach out to BP Nel Consulting for expert advice on optimizing your manufacturing process! Contact BP Nel Consulting Now.